Bryan Burkentine
Construction Management
Anthem House
Baltimore, Maryland




Click on Image to Enlarge
Photos Courtesy of The Bozzuto Construction Company
General Building Data
Building Name | Anthem House
Location & Site | Baltimore, Maryland
Building Occupant Name | Anthem House
Occupancy/Function Type | Residential Tenants, Retail Owners & Parking Garage
Apartment Building Size | 350,000 Square Feet
Retail, Garage, Apartment Building Combined Size | 540,000 Square Feet
Total Levels | 9 Floors
Date of Construction | February 2015 – April 2017
Projected Cost of Building | $75 Million
Cost Including Land, Consultants, Design, Permits | $102 Million
Project Delivery Method | Construction Manager at Risk, GMP Contract
Primary Project Team
Owner | War Horse LLC, Solstice Partners & The Bozzuto Group
Construction Manager | The Bozzuto Group
Architect | Whitman, Requardt & Associates LLP
Landscape Architect | Whitman, Requardt & Associates LLP
Interior Design | Whitman, Requardt & Associates LLP
Civil Engineer | Whitman, Requardt & Associates LLP
Structural Engineer | The SK&A Group
MEP Engineer | Environetics
Land Excavator | Iacoboni
Concrete Contractor | Miller, Long & Arnold
Structural Contractor | Infinity Structures
Electrical Contractor | Power Design
Mechanical Contractor | Mid Atlantic Air
Plumbing Contractor | Breeden Mechanical
Building Codes
Building Code | 2012 International Building Code With 2013 Baltimore City
Plumbing Code | 2012 International Plumbing Code With 2013 Baltimore City Modifications
Mechanical Code | 2012 International Mechanical Code With 2013 Baltimore City Modifications
| 2009 International Mechanical Code With 2013 Baltimore City Modifications
Electrical Code | 2011 National Electrical Code With 2013 Baltimore City Modifications
Energy Code | 2012 International Energy Conservation Code
Accessibility Codes | 2012 Maryland Accessibility Code
| Fair Housing Act of 1988
| 2010 ADA Standards For Accessible Design
Zoning Code Requirements
2012 Baltimore City Code
Architecture
The Anthem House consists of nine stories total, all on or above grade. Floors one and two on the entire West side of the building and parts of the North and South side consists of retail and restaurant space along with the top of the ninth floor (rooftop terrace) on the West side consisting of retail lounge space. While floors three through nine all consists of residential apartments. There is indeed a parking garage in the center of the building extending out fully on the North and West sides of the building on floors one through three consisting of 449 parking spaces. There are 302 residential units, varying in size, that feature 9-foot ceilings, granite countertops in kitchen, wood-like flooring, stainless steel, energy saver appliances, porcelain tiled bathrooms with granite countertops and closets, door balconies and terraces and a keyless entry system. Featured on the first and second floor will be a central fireplace, entertainment room with billiards, communal kitchen, and ample entertainment space, on-site storage, rooftop lounge and an infinity pool with over an acre of expansive green space overlooking Baltimore Harbor. The shape of the building is in an “S” shape on the upper floors to maximize the number of units with water views. This building is conveniently located in Downtown Baltimore. Also as a final note the Anthem House is not being constructed in a historical district nor does it have any historical requirements.
Building Enclosure
There are four main types of exterior walls. The first consists of 5/8 inch gypsum board over metal studs, batt insulation, gypsum sheathing, self-adhere flashing, weather barrier, 1 ½ inch rigid insulation then your brick veneer. Occasionally you have metal flashing and towards ground level the brick veneer is fully grouted in behind the brick along with waterproofing behind the grout. The two other types consist of the same materials except instead of brick there is ½ inch fiber cement board, metal standing seam shingle panel system and precast veneer. With the ½ inch fiber cement board and the metal standing seam shingle panel system there is also a 2 inch Z girt furring that goes on after the weather barrier. In addition to this furring at all 90 degree angles there is either a bent aluminum plate or MTL trim.
From the inside out the roofing consists of 5/8 inch suspended gypsum ceiling, aluminum trim, batt insulation, metal bar joist, metal decking, cover board, 4 inch rigid insulation, ¼ inch cover board and the roofing membrane. As for the green roof that is on floor three and four (courtyard space) it is on top of the structural flooring system. Therefore on top of the concrete you a protected board, waterproofing, aggregate drainage layer applied continuously along the top of foam, filter fabric, intensive lightweight planting soil, topsoil and then finally your Sod.
The window system throughout this project is an aluminum window system. The different glass types throughout the building include 1/8 inch float glass, 1/4 inch tempered glass, 1/4 inch frosted and tempered glass, 5/8 inch insulated glass which comprises of 1/8 inch tempered glass, 3/8 inch air space and 1/8 inch tempered glass, there is an insulated spandrel glass, metal panel and fire light glass. All windows that having glazing will use a low “E” glazing. This means that a low emissivity coating is applied to the glass that will reflects long wave infrared energy. Each window will have building wrap on all four sides, trim, sill flashing and jamb/head flashing. Each sash
Sustainability Features
The Anthem House will be aiming for a LEED Silver for Homes rating. LEED, Leadership in Energy and Environmental Design, is a green building accreditation platform that distinguishes the best building strategies and practices at various levels. To achieve this LEED rating of Silver the owners will need to accumulate 50-59 points. To do this The Bozzuto Construction Company will be tracking dumpster tickets for waste diverted from landfills, utilizing sustainably harvested woods and materials in the amenity areas, 112 bike storage spaces and sourcing materials within 500 miles if possible. Also the site is a brownfield, which means that it is a site that has a possible existence of harmful substances, pollutants or contaminants. In this case Bozzuto is remediating and hauling possible contaminates away to the proper facilities. A few other unique features that are in this building is that there are two elevated courtyards on the third and fourth floors with a pool, bar/lounge, cookout space and indigenous plants. There are also pet friendly amenities like a dog park and a pet wash.
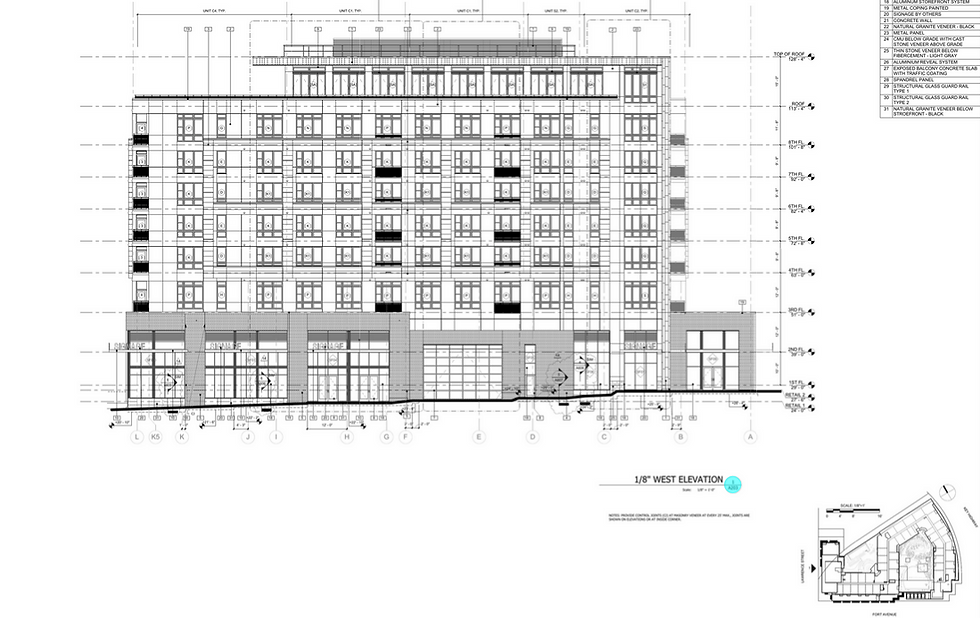

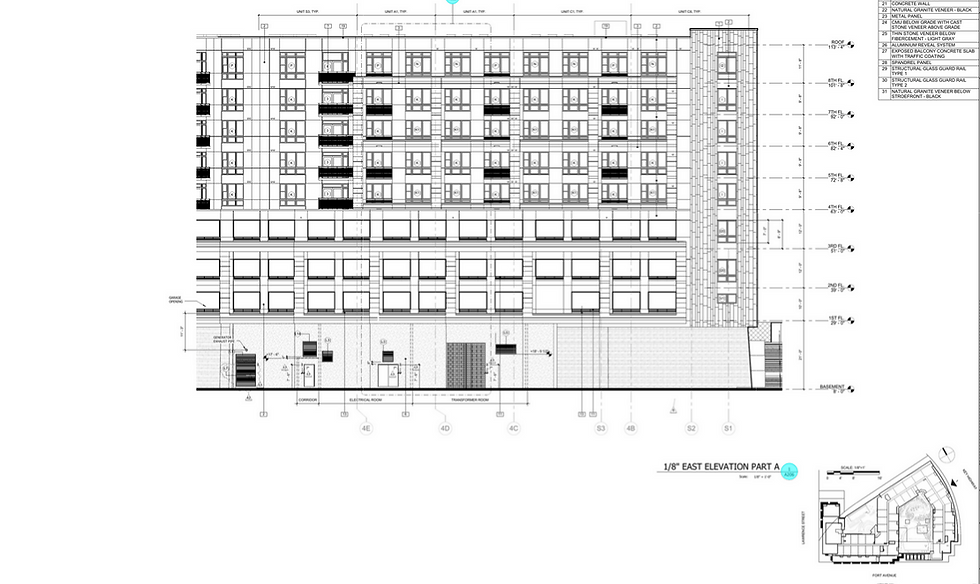
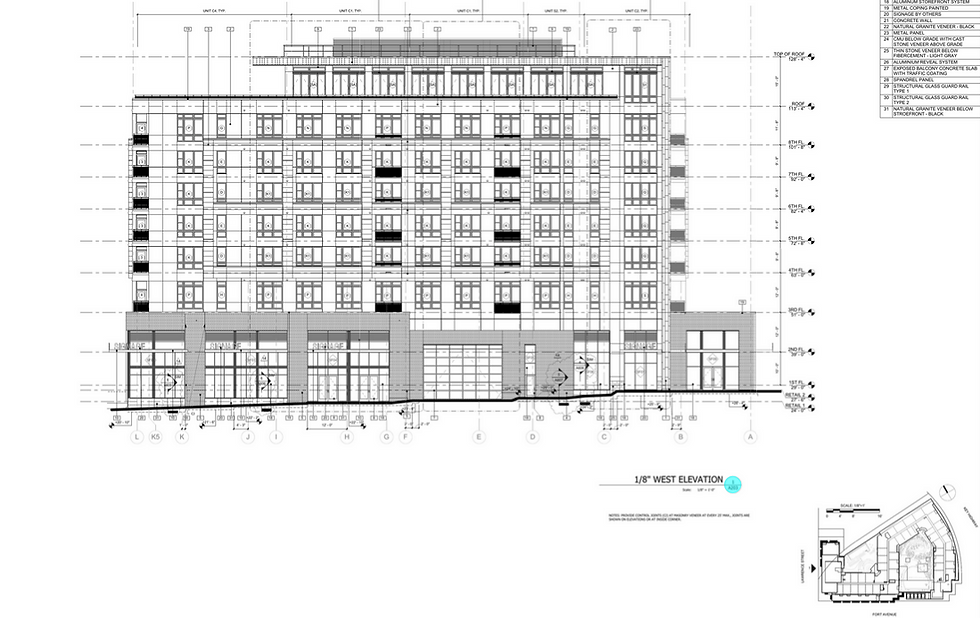
Click on Image to Enlarge
BUILDING STATISTICS- PART I
BUILDING STATISTICS- PART II
Construction
The contract for the Anthem House is a Guaranteed Max Price with a Construction Manager at Risk. The Bozzuto Construction Company was awarded the project as the Construction Manager promising a guaranteed maximum price of $102,000,000. Other major players in the project involve Miller, Long and Arnold which are doing all the concrete and structural work, while also Whitman, Requardt and Associates LLP have done all the designing and civil engineering work. Since the Anthem House is located in the heart of a large city, site congestion and access requires careful and intricate consideration. The construction manager was able to use a parking lot across from the site for their trailer, allowing smaller trailers to fit within the boundary of the site for subcontractors. This ultimately created more space for the site.
Aside from maintaining a schedule and a budget, ensuring the safety of the public took main priority. When it came to closing down the street to unload trucks or pump concrete, vehicle and pedestrian traffic where of main concern. After establishing a plan of action for safety and finalizing contract details and finances, construction began on February 23, 2015 with an expected substantial completion date in early April 2017.
Demolition
The site is to remove and cap off utilities that are on the site such as light poles. Since this site is fairly open there is not a tremendous amount of demolition to be done. Things like removing patches of 8” thick bituminous paving, portions of guard rail, trees and bushes, a bench, chain link fence, a flag pole, concrete walks, and a concrete apron are to be demolished and when needed are recycled. Contaminated soils exist on/next to the bituminous paving on the site and are to be removed with very specific instructions.
Structural
This structural consists of reinforced concrete columns coming out of the first floor spread footings. Each spread footing has either a 24” x 30” or 16” x 60” column extending from it while the columns on the second floor are 24”x24”. The slab on grade consist of a 4000 psi, 6” thick slab. Engineered pre-fabricated load-bearing structural steel panels for the walls and corrugated metal pans that will have concrete poured on them to make up the ceilings and floors (composite deck system) will be used on floors three through nine. The 14 gage metal stud walls are 3 5/8” galvanized studs spaced 16” on center. Floors three through nine receive a 3000 psi, 4 ½” thick slab reinforced with 6’ x 6’ wire mesh segments and A610 rebar. These pre-panelized load-bearing metal stud walls are pre-fabricated off site in a special facility that have a very high quality control program from welded connections to measurements. The metal pans that are being used as the decking are an Epicore MSR composite floor system that works hand-in-hand with the pre-fabricated load-bearing walls. The pans shape is flat across the bottom, which will form a constant uniform load on the bearing walls. Also on this pan are dovetail ribs that are staggered when placed on the floor with the ends of these ribs pinched. This helps reject the fire, sound and smoke transfer form unit-to-unit. All materials will be placed on site by one of two tower cranes on site.
Mechanical & Fire Protection
The main rooms for mechanical equipment are Room 201 which houses the pool pump, Room U304 which is the mechanical room for the units and Room U106a where the fire pump is. All apartments, offices, retail spaces and retail lounges will have their own separate air handling units combining to 324 units. Each apartment has its own air cooled condensing unit located on the roof. Depending on the square foot of the apartment the units range from 2-5 tons. With the air cooled condensing units each apartment has its own gas furnace with direct expansion cooling. A wet sprinkler system will be used throughout the entire building for fire suppression unitizing ½” recessed pendant sprinkler heads. Fire extinguishers will be supplied in every apartment.
Electrical System
On the lower elevation of the building is a walk out basement level where in Rooms 001, 002, 003 there is a transformer room, electric room and generator room. Coming into the electric room are two 3000A 120/208V, 3-phase, 4-wire connections. There are two to satisfy each side of the building and each has an 8 set of 4 #500 KCMIL, #400 KCMIL GND in 4 inch conduit. There are 6 meter banks, two on the fourth, sixth and eight floors. In the generator room there is a 300KW, 480V, 3-phase, 4W Diesel generator with a weatherproof enclosure.
Masonry & Exterior Facade Materials
The exterior facades have a variety of materials including fiber cement panel’s colored hardie and nichiha, masonry veneer brick colored brown and gray, vertically textured and smoothed cast in place concrete wall, black natural granite veneer, metal panel, cast stone veneer, thin stone veneer, aluminum reveal system and spandrel panel. Masonry and stone facades will be placed using galvanized metal anchors. Traditional scaffolding, tube and clamp, will be used to erect the masonry. JLG lifts will be used to place the other materials such as the fiber cement panels.